THE Piston on the VeloSoleX S
3800 is
already quite a lightweight affair and there is little
real advantage to be gained in shortening the piston by removing
some of the Piston Skirt.
In fact doing so will increase the "rocking"
(or "piston slap") and general wear within
the cylinder. A shorter piston also requires a smaller
gap between piston and cylinder to reduce this effect. Too
short a Con-Rod also increases cylinder wear. The
reason for reducing the weight of the Piston or Con-Rod is to try to relieve the crank of as much inertial
load as possible, thus giving increased Acceleration
(lighter components) but this does NOT necessarily
mean increased Top Speed.
If your engine has the Long
Piston shown below (49.45
mm long [measured at the edge] for cylinders
made before March
1986 such as the TUM 80 [V1], TUM 80A [V2]
or TUM 80A CM 6,5 [V3]), a slight increase
in Torque (but not top speed) can be obtained
by filing some metal from the Piston Skirt nearest the
Inlet Port in the shape of a Crescent
20 mm wide
and 2.5 mm high. No more should be removed
otherwise
the Exhaust Port may be partially open beneath
the piston at TDC, allowing the old exhaust gases to enter
the crankcase and pollute the fresh mixture. You can undo this modification
by replacing the piston with a new one OR by turning
the piston 180° around by
removing the Crank Pin (Big-End)
Bolt and turning the Con-Rod by half a turn before replacing Crank
Pin (Big-End) Bolt. To stop the flywheel turning when loosening or tightening the Crank Pin (Big-End) Bolt, fit a Flywheel Clamp.
After
you have modified the Piston Skirt,
drill out the Inlet Port hole
in the side of the cylinder using a 9
mm drill.
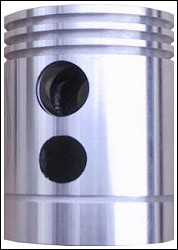
If your engine has the
Short Piston shown
below (46.98
mm long [measured at the edge] for cylinders
made after March
1986 such as the TUM M 80A CM 6,5 [V4,
M = MBK version]), there is no benefit to be gained by
filing the Piston Skirt.
Also the Inlet Port hole
in the side of the cylinder for that engine will already be 9 mm
in diameter.

A slight increase in Torque can be
obtained if the round
Transfer Holes in the piston are filed square (remembering
to leave
a slight radius in each corner). This increase in Torque is due to
a more efficient transfer of the mixture from the crankcase.
With regard to Bore/Stroke
Ratio:
- "Stroking an engine" = "increasing
the Stroke"
- "Boring an engine" = "increasing
the Bore"
- A "Square" engine means "stroke"
= "bore"
- An "Over-square" engine means
"bore" > "stroke"
- An "Under-square" engine means
"bore" < "stroke"
The VeloSoleX S
3800 is
very slightly "Under-square", a design better
for low-RPM
torque, but usually not for high-RPM horsepower. "Under-square" motors were much more common
in the pre-war period than they are today.
With regard to Rod/Stroke
Ratio on the VeloSoleX S
3800:


This high Rod/Stroke
Ratio (ie: long Con-Rod) means LESS WEAR to cylinder walls, pistons and piston rings
as the combustion forces acting in the downward
motion are increased while those toward the cylinder wall are reduced.
Also the Piston Dwell
Time is longer, meaning that piston remains at the top and bottom of the stroke
for a longer time.
This allows for better flow of combustion and exhaust
gases since the piston accelerates slower in the transition between the "up" and
"down" strokes. Intake gases have a longer time to enter the cylinder while
exhaust gases are given more time to escape. This means more
torque over a wider RPM range. On the other hand, even though the piston
accelerates slower in transition, the Maximum Piston Velocity
is greater than for a low Rod/Stroke
Ratio
resulting in some
increased component strain.
While it is true that piston
dwell at TDC is longer with a longer Con-Rod and hence a
higher combustion pressure exerted for longer on the
piston crown, it should be remembered that maximum
torque applied to the crank is when the rod to crank angle is at 90°.
When a shorter rod is used, this 90° angle is reached sooner in the engine cycle
and therefore at a higher combustion pressure due to the smaller combustion volume
at that point. So, for low-speed maximum torque a shorter rod is better,
while for high-speed maximum power a longer rod is better
(ignoring the increased rod mass for a longer rod).
In the end, it must be remembered
that the VeloSoleX engine was never designed,
regarding component tolerances and general wear, to
be a high-revving "sports" engine and many
VeloSoleX tuners have found the engine life
to be reduced considerably by excessively changing the
existing engine parameters.
|